先日完成したオーダーのジャズベースタイプの製作の様子をご紹介していきます。
こちらが製作した楽器です。
当工房オリジナルのソリッドカラーとブロックポジションがとてもカッコいい1本になったと思います。
楽器を演奏する人はもちろん、そうでない人も一度は目にしたことのあるはずジャズベース。言わずもがなフェンダー社のモデルなのですが今や世界中のメーカーがこのモデルを元に製品を作っています。完コピ系のものからオリジナルの要素を含んだものまで色々あります。
競合他社多数なジャズベースタイプなのです。
そんな数ある選択肢の中から、「鹿川に作ってもらおう。」と思っていただけたことはとてもありがたいことです。
オーダーいただけたのは、僕が作る意味、メリットをオーナー様が見出していただけたからだと思います。
ご注文いただいたときはオリジナルモデルのオーダーとはまた違った嬉しさがあったことを覚えています。(僕自身フェンダーの楽器大好きですし)
何より本家ではなく、僕にオーダーいただけたことは大変恐縮でありつつもとても光栄なことです。
基本的にフェンダー社の楽器は工場で量産を目的に作られた構造、設計ですので非常に作りやすいです。
ですが工場と僕のような個人工房設備が大きく異なりますので、ならではの難しさも有ります。そこはフェンダー愛で乗り切り、各工程魂を込めて製作しました。
それでは早速指板製作から!
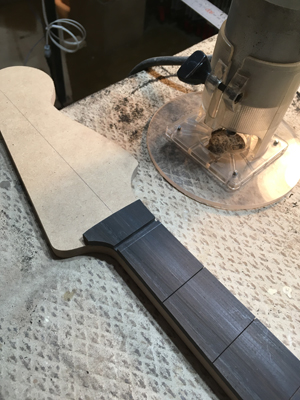
フレットの溝切り後は、いきなりフェンダータイプならではの工程です。
ネック全体の型を作り、それに合わせてトリマーを使用し指板材を加工していきます。
指板のナット上部はヘッドの形と滑らかにつながるようなラインになっています。それを再現するための工程です。
フェンダーの数あるモデルの中でもジャズベースはナット幅が狭く、ヘッドの幅が広いので特にこれが顕著です。(次の写真をご参照ください)
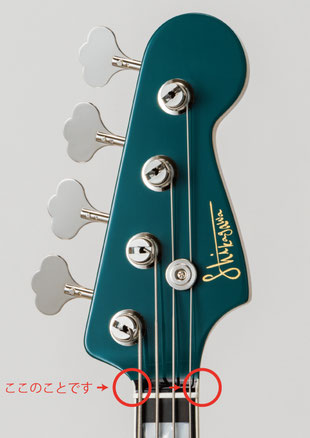
こうなっているのは恐らくフェンダーが「この指板からヘッドにかけての流れが堪んないんだよなー」と設計したわけではなと思います。ヘッドシェイプ、ナットと4弦ペグの距離といった構造的な問題や、平板段付きヘッドのネック(フェンダータイプのネックのことです)ならではの製造工程である、指板接着をしてからピンルーター(今はNCルーター)という機械を使いネックの形に加工していくという流れで『たまたまそうなった』だけのことだと思います。この工程自体1ピースネックの作り方の名残だったりします。当時のギターでは革新的な製造方法だったことと思います。
正直僕の工房の設備だとやりにくい工程でして、ナット上部まで真っすぐな方が作りやすいです。
だったらやりやすいように作ったらええがな!と思う方もいらっしゃっるかもしれませんが、本家のデティールを見慣れすぎている僕にはここを真っすぐにするなんて考えられません…!少しくらい作業しにくくてもフェンダー工場への思いを馳せながら作業すればなんてことはありません。
というわけで古き良きフェンダー工場の動画をどうぞ。
作業に戻ります…!。
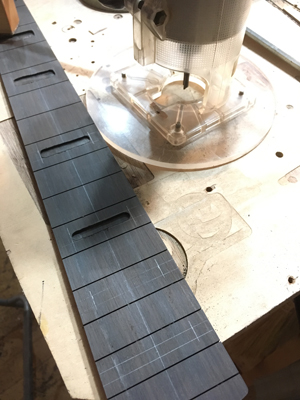
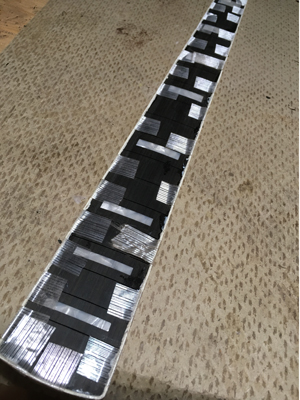
ロマンにあふれた工場の様子はいかがだったでしょうか?皆様活き活きとお仕事されていて素敵な楽器が生まれてきそうな空間でしたね。
指板の外周加工が終わったらポジションマーク入れ、バインディング接着と進んでいきます。
ポジションマークはパーロイドの板材から1つずつ削り出します。そしてそれぞれにピッタリなザグリを指板側にも掘っていきます。バインディング接着には引っ張り方向に強いフィラメントテープを使い、しっかりと貼り付けていきます。
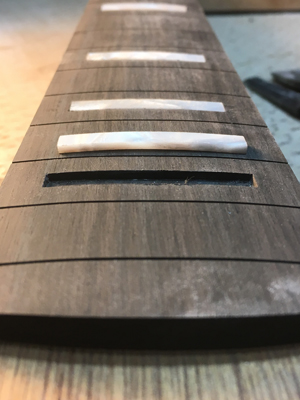
ブロックポジションの入れ方にも一工夫。今回は指板表面に少しきつめのRが付くので、ポジションの材料であるパ
パーロイドはどうしても透けてしまう素材なのでこの埋め方をした方が
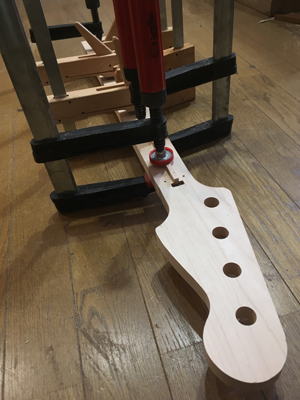
ネックの状態に切り出し、グリップ部分も仮加工。仕上がりに近い状態に削り込んでネック材の狂いを出し、修正したうえでトラスロッドを仕込みます。
ここは本家と違う流れになりますが、この方法のほうがより精度の高いネックができると思います。
ハンドメイドならではですね。
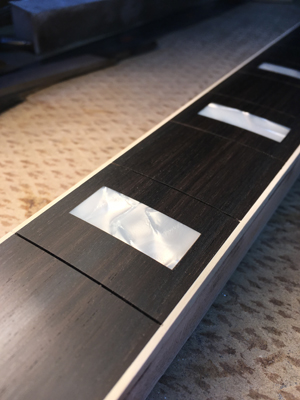
その後指板接着を経てフレット打ちの準備です。
毎度のことですが、闇雲に指板表面を磨いているわけではなく縦方向の直線、横方向のR、表面のキズの3つの要素をすべて整えながら成形していきます。
ブロックポジションも綺麗に入っていて一安心。
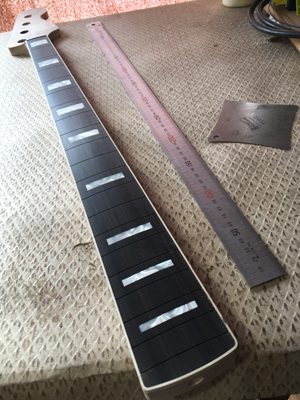
ネックらしくなってきました。
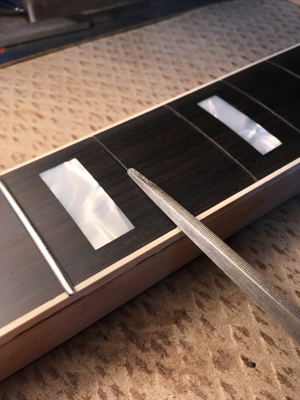
フレット打ちとは言いますが打つ工程よりもその前の準備をしっかり行うことが重要です。
これはフレットが入り込む溝の入り口を面取りしているところです。
先の指板表面の状態もそうですが、大体こんくらいでいいやと次の工程に進むと状態の良いネックにはなりにくいです。
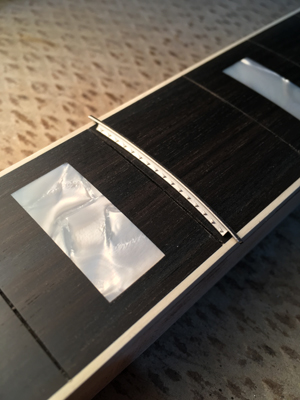
更に今回はバインディング有の仕様なのでフレットの端のタング部分を少し削り落とします。オーバーバインディング加工といわれるやつです。
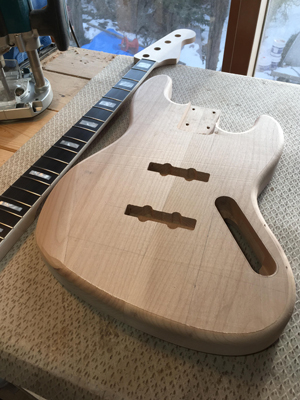
無事フレットも打ち終わりまして、いつの間にかボディが出来上がっています。
次回はボディ製作編をご紹介いたします!